Why plastic extrusion is ideal for mass production
Why plastic extrusion is ideal for mass production
Blog Article
Recognizing the Basics and Applications of Plastic Extrusion in Modern Production
In the realm of contemporary production, the strategy of plastic extrusion plays an instrumental duty - plastic extrusion. This intricate process, including the melting and shaping of plastic via specialized passes away, is leveraged throughout different markets for the production of varied products. From car parts to consumer items packaging, the applications are huge, and the potential for sustainability is equally outstanding. Unraveling the principles of this procedure exposes the real flexibility and potential of plastic extrusion.
The Fundamentals of Plastic Extrusion Process
While it may show up complex, the basics of the plastic extrusion procedure are based on relatively straightforward principles. It is a production procedure where plastic is melted and then shaped right into a continuous profile with a die. The raw plastic product, frequently in the type of pellets, is fed into an extruder. Inside the extruder, the plastic goes through heat and stress, triggering it to thaw. The liquified plastic is then required with a designed opening, called a die, to develop a long, continual product. The extruded item is cooled and after that cut to the wanted length. The plastic extrusion procedure is thoroughly made use of in various sectors because of its efficiency, cost-effectiveness, and convenience.
Different Sorts Of Plastic Extrusion Techniques
Structure upon the fundamental understanding of the plastic extrusion process, it is essential to discover the different techniques entailed in this production technique. In contrast, sheet extrusion creates large, flat sheets of plastic, which are commonly more refined right into items such as food product packaging, shower drapes, and vehicle parts. Understanding these methods is key to using plastic extrusion properly in contemporary production.
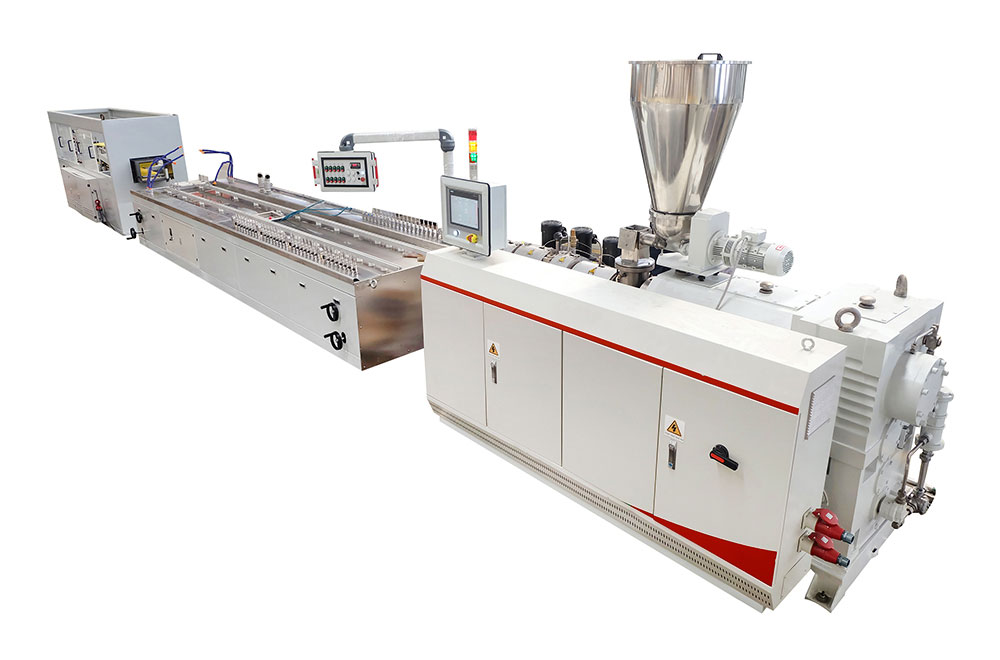
The Role of Plastic Extrusion in the Automotive Industry
A frustrating bulk of components in modern cars are items of the plastic extrusion procedure. This process has changed the auto market, transforming it into a more reliable, affordable, and versatile production industry. Plastic extrusion is mainly made use of in the manufacturing of numerous vehicle elements such as bumpers, grills, door panels, and dashboard trim. The procedure offers an uniform, constant result, allowing suppliers to generate high-volume get rid of great precision and very little waste. The agility of the extruded plastic parts adds to the total reduction in car weight, improving fuel effectiveness. Moreover, the resilience and resistance of these parts to warm, cool, and effect improve the durability of automobiles. Hence, plastic extrusion plays a crucial role in vehicle production.
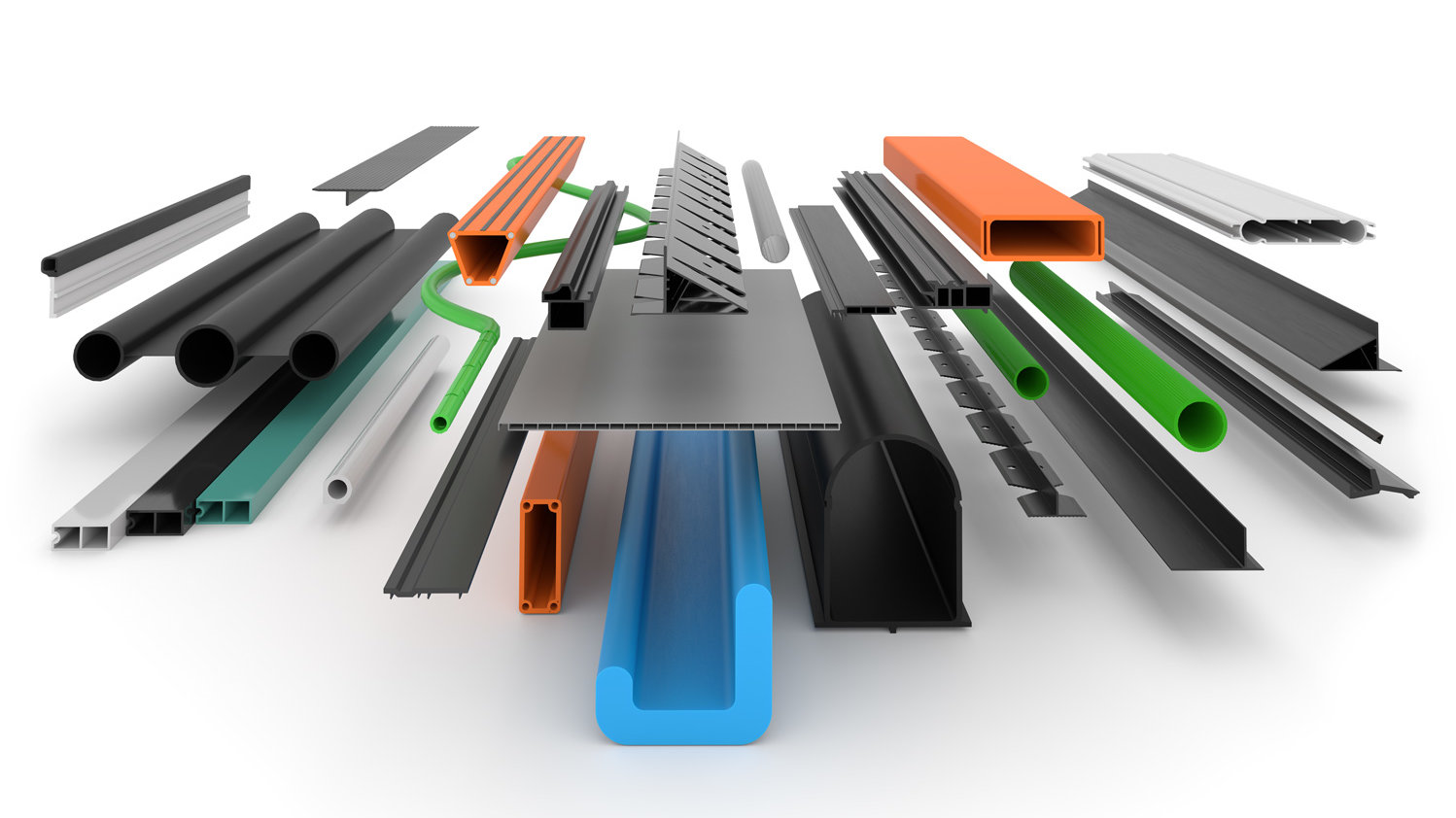
Applications of Plastic Extrusion in Customer Item Manufacturing
Past its considerable impact on the automobile sector, plastic extrusion verifies equally effective in the world of customer products making. The Recommended Reading versatility of plastic extrusion permits manufacturers to design and generate intricate shapes and dimensions with high accuracy and performance. The adaptability, versatility, and cost-effectiveness of plastic extrusion make it a recommended selection for numerous consumer items producers, adding significantly to the market's growth and development.
Environmental Influence and Sustainability in Plastic Extrusion
The prevalent usage of plastic extrusion in manufacturing welcomes analysis of its ecological ramifications. Effective machinery decreases energy usage, while waste monitoring systems reuse scrap plastic, reducing raw material needs. Regardless of these improvements, additionally development is required to mitigate the ecological footprint of plastic extrusion.
Conclusion
In final thought, plastic extrusion plays a crucial function in contemporary manufacturing, specifically navigate to this website in the automobile and customer products sectors. Comprehending the basics of this process is crucial to maximizing its applications and advantages.
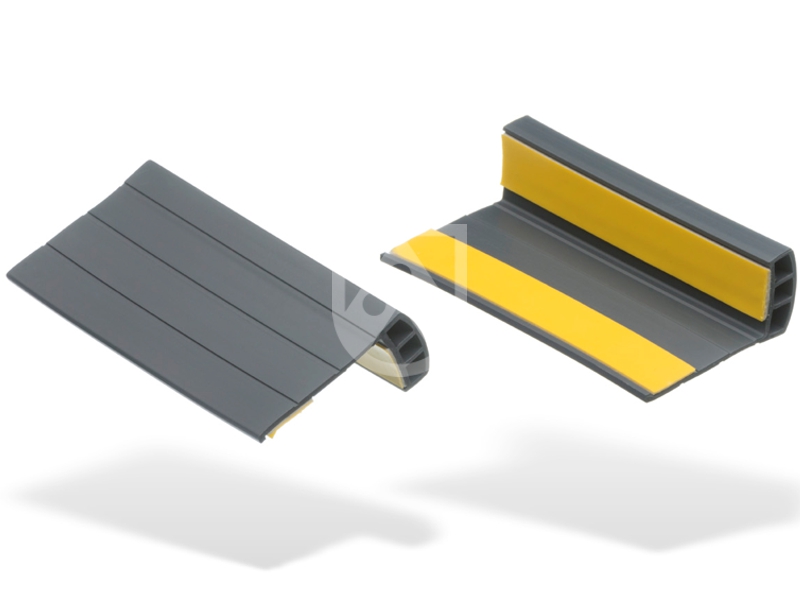
The plastic extrusion process is thoroughly utilized in different markets due to its efficiency, cost-effectiveness, and versatility.
Building upon the standard understanding of the plastic extrusion process, it is needed to explore the various strategies involved in this manufacturing technique. plastic extrusion. In contrast, sheet extrusion develops huge, level sheets of plastic, which are generally more processed into products such as food straight from the source packaging, shower curtains, and car components.An overwhelming majority of components in modern cars are items of the plastic extrusion process
Report this page