The Best Strategy To Use For Alcast Company
The Best Strategy To Use For Alcast Company
Blog Article
The Best Strategy To Use For Alcast Company
Table of ContentsAlcast Company Can Be Fun For AnyoneThe Main Principles Of Alcast Company An Unbiased View of Alcast CompanyThe Buzz on Alcast CompanyAlcast Company - QuestionsThe Of Alcast Company
The refined distinction depends on the chemical material. Chemical Contrast of Cast Aluminum Alloys Silicon promotes castability by decreasing the alloy's melting temperature level and boosting fluidity during casting. It plays an essential role in allowing detailed molds to be filled precisely. Furthermore, silicon adds to the alloy's toughness and use resistance, making it beneficial in applications where durability is crucial, such as automobile components and engine elements.It additionally enhances the machinability of the alloy, making it less complicated to refine into finished products. In this way, iron adds to the total workability of light weight aluminum alloys.
Manganese adds to the strength of light weight aluminum alloys and boosts workability (Casting Foundry). It is generally utilized in functioned light weight aluminum products like sheets, extrusions, and accounts. The visibility of manganese help in the alloy's formability and resistance to fracturing during fabrication processes. Magnesium is a lightweight component that provides toughness and effect resistance to aluminum alloys.
Some Ideas on Alcast Company You Should Know
Zinc improves the castability of aluminum alloys and assists regulate the solidification procedure throughout casting. It improves the alloy's strength and firmness.

The key thermal conductivity, tensile toughness, return toughness, and prolongation vary. Among the above alloys, A356 has the highest thermal conductivity, and A380 and ADC12 have the lowest.
Our Alcast Company PDFs
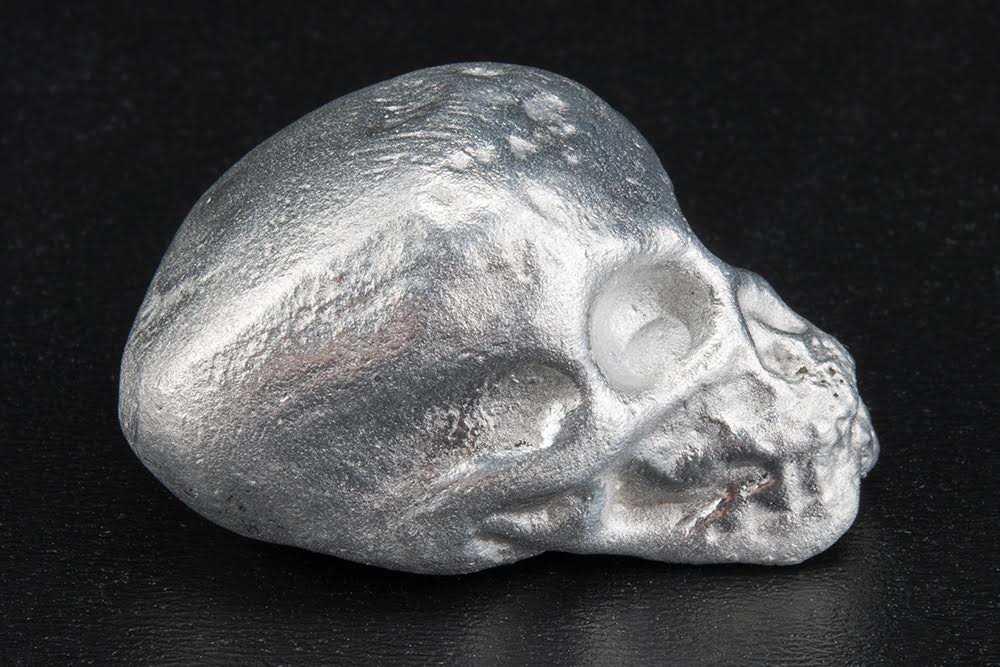
In precision spreading, 6063 is fit for applications where elaborate geometries and top quality surface area coatings are extremely important. Instances consist of telecommunication enclosures, where the alloy's exceptional formability permits smooth and cosmetically pleasing designs while preserving structural stability. In a similar way, in the Lighting Solutions sector, precision-cast 6063 elements create sophisticated and reliable lights components that require detailed shapes and great thermal efficiency.
It results in a better surface area coating and far better deterioration resistance in A360. Furthermore, the A360 exhibits premium elongation, making it optimal for complex and thin-walled parts. In accuracy spreading applications, A360 is appropriate for markets such as Consumer Electronic Devices, Telecommunication, and Power Devices. Its boosted fluidness enables elaborate, high-precision components like smartphone casings and communication tool housings.
The Ultimate Guide To Alcast Company
Its unique residential or commercial properties make A360 a useful choice for precision spreading in these industries, enhancing item resilience and high quality. Aluminum alloy 380, or A380, is an extensively used casting alloy with a number of unique characteristics. It uses superb castability, making it an optimal option for precision casting. A380 exhibits great fluidness when molten, guaranteeing complex and comprehensive molds are accurately recreated.
In precision spreading, light weight aluminum 413 shines in the Customer Electronic Devices and Power Tools industries. This alloy's superior rust resistance makes it an exceptional selection for exterior applications, making sure lasting, sturdy items in the discussed sectors.
How Alcast Company can Save You Time, Stress, and Money.
As soon as you have made a decision that the aluminum die casting process is ideal for your job, an important following step is choosing the most appropriate alloy. The aluminum alloy you choose will significantly affect both the casting procedure and the residential properties of the end product. Due to this, you must make your decision carefully and take an informed method.
Figuring out the most suitable aluminum alloy for your application will indicate evaluating a wide selection of features. The very first category addresses alloy features that impact the manufacturing procedure.
The Best Guide To Alcast Company
The alloy you choose for die spreading straight impacts several elements of the spreading procedure, like exactly how very easy the alloy is to deal with and if it is prone to casting defects. Warm breaking, additionally understood as solidification breaking, is a regular die casting issue for aluminum alloys that can lead to inner or surface-level tears or fractures.
Particular light weight aluminum alloys are much more at risk to hot breaking than others, and your choice must consider this. It can damage both the actors and the die, so you must look for alloys with high anti-soldering homes.
Rust resistance, which is currently a noteworthy quality of aluminum, can differ considerably from alloy to alloy and is a vital particular to take into consideration depending on the ecological problems your item will be exposed to (Foundry). Put on resistance is another home commonly looked for in light weight aluminum items and can set apart some navigate to this site alloys
Report this page